SUSS Training Center Garching
Improve your production efficiency in our 600 m² facility
Our Training Center at our headquarters in Garching near Munich offers further training and practical courses for our SUSS production systems, which are in demand worldwide. Whether you are a new customer or a long-standing partner looking to expand your existing knowledge, we have the right offer for you to take your production efficiency to the next level.
Customized training in small groups
Our comprehensive learning courses are tailored to the needs of the following professionals:
- Tool Operator
- Process Engineer
- Equipment & Maintenance Engineer
We keep our training groups very small to ensure calm and concentrated learning and allow each participant to work and learn independently on our machines. Our team of trainers will answer individual questions and take the time to focus on the respective priorities.
Our customers particularly appreciate the SUSS Training Center for:
- Dedicated training equipment for hands-on practice
- Modern facilities
- Quiet learning atmosphere for concentrated and efficient learning
- Good transport connections for convenient arrival and departure
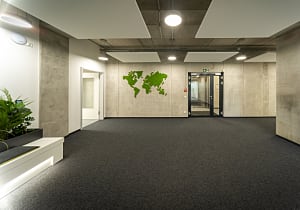
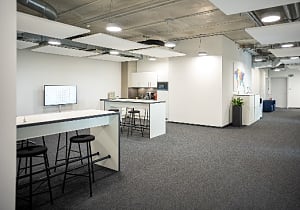
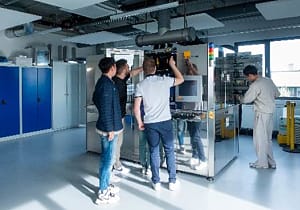
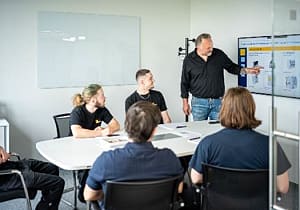
Learning environment
The SUSS Training Center has expanded and moved into new premises.
- 350 m walking distance to the SUSS headquarters in Garching near Munich
- 4 training areas over an area of 600 m²
- Coffee lounge
- Customer parking spaces in front of the building
Training contents
The following courses are available for each machine type:
Operator
Introductory course for a basic overview of structure and function. Teaches safe and efficient operation of the system for successful production operation.
Process settings
Learning module for process engineers for the independent development and optimization of production processes. Provides a good understanding of the process sequences within the production system and the creation of automatic procedures. Teaches all process-relevant parameters and their settings.
Maintenance
Learning module for equipment technicians and engineers for high-volume operation of the production system. Provides a good overall understanding of equipment functionality and the interaction of individual components. Teaches maintenance procedures and how to troubleshoot the most common issues for high up-time.
Contact
If you are interested in a training course, please contact us. We will get back to you, to discuss training content and schedule, arrange an individual appointment and support you with your travel arrangements. Whatever your (training) needs are, our team is happy to assist you.
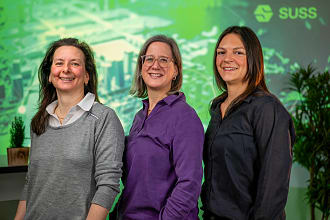
Training Center Office
85748 Garching near Munich
Germany